Compcut ACS 1200
The Compcut ACS 1200 advanced composite plate saw achieves precise cutting in a diverse range of materials to prepare highly accurate composite test specimens. This is the largest machine in the range – with a clear panel size of 1200 mm x 1200 mm – perfect for larger laminate sizes and test specimens.
1200 x 1200 MM
Cleared Panel Size
4500 RPM
Max Spindle Speed
2.4 KW
Spindle Power
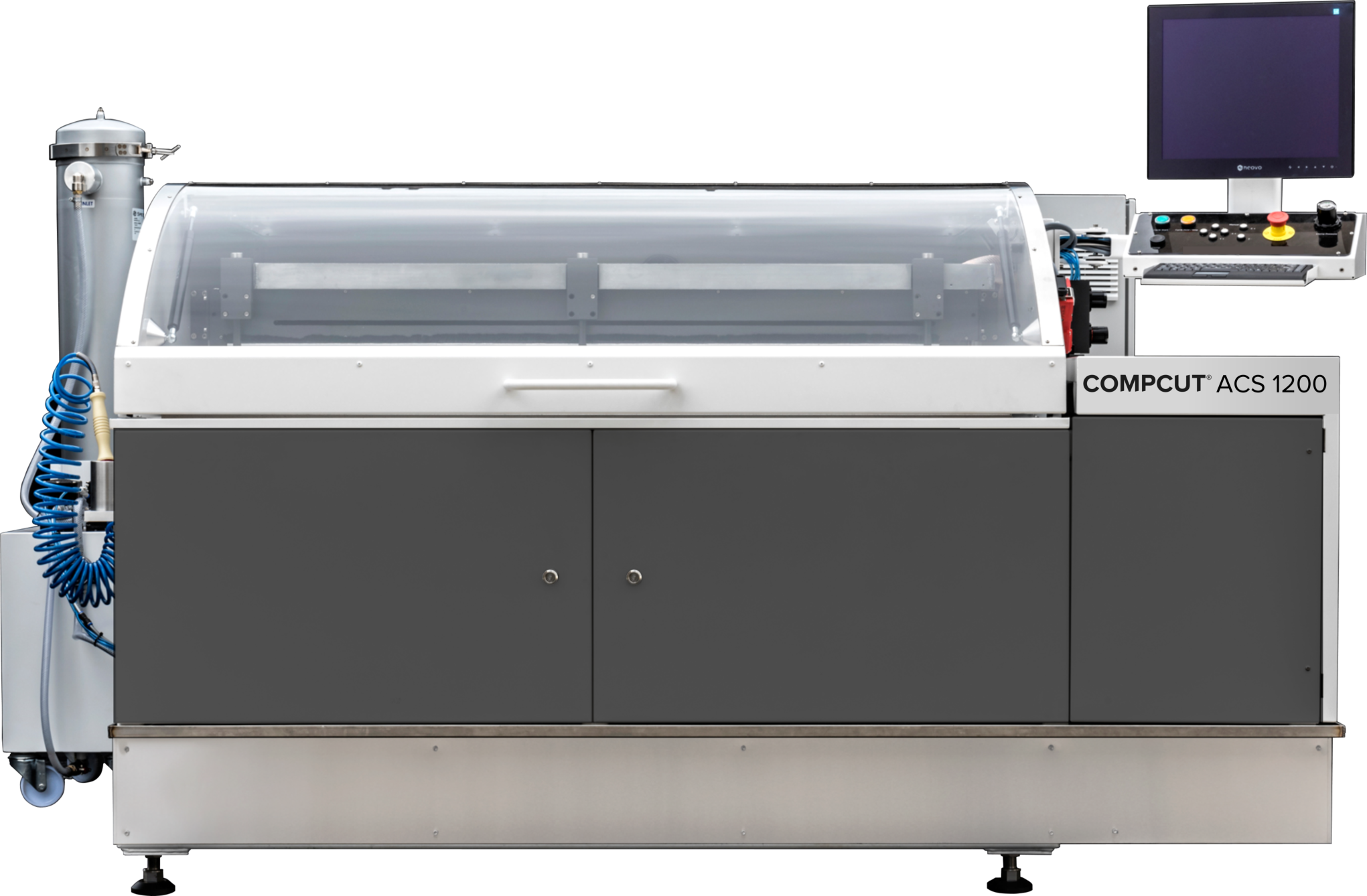
CNC MATERIAL FENCE
- Pneumatic sheet clamps to clamp a wide range of materials
- Automatic positioning for repeat production without user intervention
- Dual driven for exceptional perpendicularity & parallelism
- Repeatable
CROSS-CUT CARRIAGE
- Rigidity of X-axis assembly provides superior surface finish
- Clear working area with cutting head below the table
- Easy blade change
- Servo-driven ball screw provides smooth and accurate cutting feed
BAR CLAMP WITH COOLANT
- Both laminate and cut specimen are secured during the cutting process
- Constant flood cooling across entire cut length
USER INTERFACE CONTROL SYSTEM
- Conversational CNC permits ease of use
- Part-programmable for automatic machining
- Material parameters store best feed and spindle speeds for each laminate
- Remote support available
COOLANT SYSTEM
- Bag-based filter system for easy maintenance
- Washdown lance for easy cleaning
- Recirculating or a 100 loss systems
- Able to use multiple coolants
SAFE WORKING ENVIRONMENT
- Fully enclosed work area
- Connection to external dust extractor
- CE marked to relevant standards
- Fully interlocked system
- Bag-based filter system for easy maintenance
SPECIFICATIONS
Material Capacity | |
---|---|
CLEARED PANEL SIZE |
1200 X 1200 MM @20 MM |
MATERIAL THICKNESS/CUT DEPTH* |
0 – 50 MM / 0 – 100 MM |
FRONT SPECIMEN TABLE |
400 MM |
COOLANT CAPABILITY |
FLOOD COOLANT WITH BAG FILTER |
Enclosure | |
ENCLOSURE |
FULLY ENCLOSED – EXTRACTABLE |
Spindle | |
SPEED | 2000 TO 4500RPM |
SPINDLE POWER | 2.4KW |
BLADE SIZE | 300 – 400MM |
BLADE THICKNESS | 1.5 – 4.5MM |
Speeds | |
RAPID SPEEDS X,Y,Z | 125 MM/S |
CUTTING SPEEDS | 0.1 – 40MM/S |
Accuracy, Perpendicularity, Parallelism | |
TYPICAL SPECIMEN PERPENDICULARITY | 0.03 MM |
TYPICAL SPECIMEN PARALLELISM / 100MM* | 0.03 MM |
TYPICAL SPECIMEN PARALLELISM / 300MM* | 0.04 MM |
TYPICAL SPECIMEN PARALLELISM / PANEL | 0.08 MM |
TYPICAL SPECIMEN DIMENSIONAL ACCURACY |
0.05 MM |
TYPICAL SPECIMEN PARALLELISM Z PLANE |
0.03 DEG |
External Dimensions: (W)x(D)x(H) | |
WIDTH* | 2150 MM |
DEPTH* | 2470 MM |
HEIGHT* | 1650 MM |
Required Services | |
POWER | 415V 3PH 32A |
AIR – DRIED & FILTERED | 70- 125 PSI |
EXTRACTION | APPLICATION SPECIFIC |
Success at CTE
CTE comes fully equipped to test the latest composite, adhesive, and other non-metallic materials and components, with a wide array of evaluation services and equipment that Compcut material cutters have greatly supplemented. Two Composite Plate Saws (the Compcut CPS 200 and CPS 1000) are currently in use by the centre, including a Precision Composite Router (PCR 300) that all make up most of the facility’s equipment for delivering high quality specimen manufacturing.
CTE has many years of experience in evaluating parts for industries such as aerospace, construction, automotive, and environment, testing non-metallic materials for over ten years and upholding a deep and meticulous understanding for composite material tensile strength, durability, and finish against traditional metals.
Utilising Sharp & Tappin’s range of Compcut machines, Composite Test and Evaluation confidently offers reliable, cost-effective, and timely qualifications for a variety of composite samples—materials relevant to our Compcut challenge.
A Cut Above the Rest
Our Compcut saws have gained exceptional results in recent tests at CTE. In just 11 hours, CPS machines were able to efficiently cut 842 composite specimens—that’s 1 specimen that was machined and ready to test every 47 seconds. In comparison, the time in which to cut the same specimens from a manual saw, such as a modified tile cutter, would take more than 5 minutes per specimen when accounting for setup and post preparation of the composite material.
From previous tests conducted for the National Composites Centre (NCC), in which the Precision Composite Router 500 was used to cut dog-bone shaped specimens from Ceramic Matrix Composite material (CMC), Sharp & Tappin has set the standard for clean and reproduceable finishes at Composite Test and Evaluation, with a near zero scrap rate.
CTE initially tested the Compcut machines before overwhelming results in successful trials was followed by their subsequent purchases. Paul Yeo, Managing Director of CTE, has spoken about Compcut’s innovation; “We recently machined 240 laminates into 3840 specimens and did not lose one specimen due to it being out of tolerance. As well as the reproducibility on show, these specimens were cut into a variety of component types, all varying in size and shape, reaffirming the great efficiency Sharp & Tappin’s Compcut machines provide.” The specimens produced on the saws exceeded requirements of the common international standards that CTE perform testing to.
Our latest generation of Compcut saws perform at such a high quality of manufacture that post preparation of composite materials, usually made to remove machining marks, is not required as the Composite Plate Saws leave exceptional edge finish in half the time preparation takes. CTE are thus able to offer its customers significant cost benefits at a reduced timescale, improving the flow of manufacture and increasing the scale of production.
“The 3840 specimens we recently tested provided us with sufficient results to compare against our operating processes,” said Paul. “It saved us 4 weeks of labour and programming time due to the redundancy of post preparation. The time it takes to cut composite materials has now been greatly reduced, meaning customers will not only have their requests seen to quicker, but will receive their products on time and with the highest quality of cutting precision.”