Compcut ACS 300
The Compcut ACS 300 advanced composite plate saw achieves precise cutting in a diverse range of materials to prepare highly accurate composite test specimens. This is the smallest of the range – with a clear panel size of 300 mm x 300 mm – perfect for smaller laminate sizes and test specimens.
300 x 300 MM
Cleared Panel Size
4500 RPM
Max Spindle Speed
1.5 KW
Spindle Power
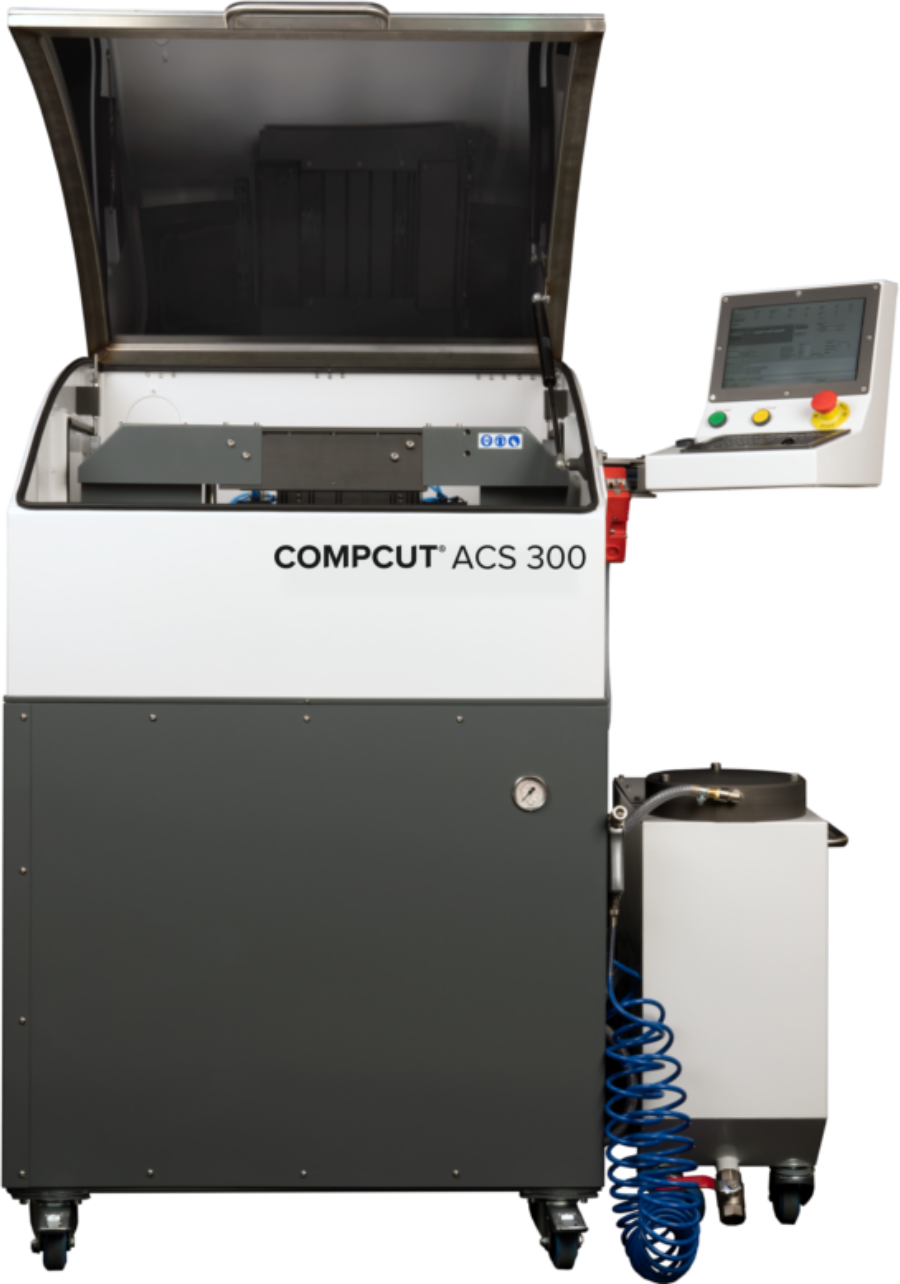
CNC MATERIAL FENCE
- Pneumatic sheet clamps to clamp a wide range of materials
- Automatic positioning for repeat production without user intervention
- Dual driven for exceptional perpendicularity & parallelism
- Repeatable
CROSS-CUT CARRIAGE
- Rigidity of X-axis assembly provides superior surface finish
- Clear working area with cutting head below the table
- Easy blade change
- Servo-driven ball screw provides smooth and accurate cutting feed
BAR CLAMP WITH COOLANT
- Both laminate and cut specimen are secured during the cutting process
- Constant flood cooling across entire cut length
USER INTERFACE CONTROL SYSTEM
- Conversational CNC permits ease of use
- Part-programmable for automatic machining
- Material parameters store best feed and spindle speeds for each laminate
- Remote support available
COOLANT SYSTEM
- Bag-based filter system for easy maintenance
- Washdown lance for easy cleaning
- Recirculating or a 100 loss systems
- Able to use multiple coolants
SAFE WORKING ENVIRONMENT
- Fully enclosed work area
- Connection to external dust extractor
- CE marked to relevant standards
- Fully interlocked system
- Bag-based filter system for easy maintenance
SPECIFICATIONS
Material Capacity | |
---|---|
CLEARED PANEL SIZE | 300X300MM |
MATERIAL THICKNESS/CUT DEPTH* | 0 – 20 MM OR 0 – 30 MM |
FRONT SPECIMEN TABLE |
350 MM |
COOLANT CAPABILITY |
FLOOD COOLANT WITH BAG FILTER |
Enclosure | |
ENCLOSURE |
FULLY ENCLOSED – EXTRACTABLE |
Spindle | |
SPEED | 2000 TO 4500RPM |
SPINDLE POWER | 1.5KW |
BLADE SIZE | 200 – 250MM |
BLADE THICKNESS | 1.5 – 3.5MM |
Speeds | |
RAPID SPEEDS X,Y,Z | 60MM/S |
CUTTING SPEEDS | 0.1 – 40MM/S |
Accuracy, Perpendicularity, Parallelism | |
TYPICAL SPECIMEN PERPENDICULARITY | 0.03 MM |
TYPICAL SPECIMEN PARALLELISM / 100MM* | 0.03 MM |
TYPICAL SPECIMEN PARALLELISM / 300MM* | 0.04 MM |
TYPICAL SPECIMEN PARALLELISM / PANEL | N/A |
TYPICAL SPECIMEN DIMENSIONAL ACCURACY |
0.05 MM |
TYPICAL SPECIMEN PARALLELISM Z PLANE |
0.03 DEG |
External Dimensions: (W)x(D)x(H) | |
WIDTH* | 1220 MM |
DEPTH* | 1040 MM |
HEIGHT* | 1500 MM |
Required Services | |
POWER | 220V 1PH 16A |
AIR – DRIED & FILTERED | 70- 100 PSI |
EXTRACTION | APPLICATION SPECIFIC |
A TESTING TRANSFORMATION:
R-TECH MATERIALS
Based in Margam in South Wales, R-Tech Materials enjoy a global reputation as a materials testing and consultancy business, offering a unique blend of accredited testing services together with extensive industrial experience and materials knowledge covering a diverse range of industries
R-Tech’s Materials Testing Division were keen to explore the introduction of a Compcut 300 Plate Saw to support and enhance the work of their composites team enabling the creation of highly accurate test laminates specimens integral to their composites testing processes. The company feel strongly that specimen extraction is a critically important element in any comprehensive test regime.
Dr Geraint Havard, R-Tech’s Composite Manager comments, ‘Our exploration into the Compcut technology was very much driven by our prior experience of cutting samples, using a tile saw with a diamond blade – a time consuming and often inaccurate process with variations in output consistency. In addition to technical performance we were also attracted to the user safety aspects of the Compcut unit, as being an ISO 45001 accredited company we place great emphasis on staff health and safety.’
Already aware of the Compcut 300’s reputation and outline specifications, R-Tech were able to witness a ‘live’ demonstration of the machine’s practical capabilities on the Compcut stand at the 2019 Advanced Engineering Show. The R-Tech team were able to furnish a selection of their own material samples and experience for themselves the Compcut’s capability to speedily cut test samples to extremely high standards of accuracy and repeatability.
Impressed by both the practical demonstration and interaction with Compcut’s uniquely intuitive and easy to use operating system, the Material’s Testing Division acquired their Compcut 200 in December 2020. The unit is situated at R-Tech’s Test House in Port Talbot. Compcut’s Kevin Tappin supervised the delivery, installation and commissioning of the unit on site, a challenge in itself with strict social distancing guidelines in place!
The unit was immediately put to work helping to streamline R-Tech’s specimen production process, enabling the entire technical team to rapidly and repeatedly produce specimens to a consistently high standard – at a stroke doing away with the previous time consuming practice of having different operators produce varying standards of specimens!
Dr Geraint Havard, R-Tech’s Composite Manager comments, ‘Following the introduction of the Compcut 300, we have already come to regard it as a vital asset in helping to streamline our composite test specimen production flow. Its intuitive operating system has immediately allowed our technical team to readily engage with the machine – rapidly producing specimens to the highest standards of accuracy and repeatability.
We are currently able to consistently produce a wide range and quantity of samples all to a uniform and consistent standard.
All of which are major factors towards underpinning and ensuring the reliable consistency of all our test results both now and into the future as we further expand our award winning test lab services.’
NB. Dr Havard has a background in mechanical and materials engineering and was ‘Composites UK Employee of the Year’ in 2020