Compcut PCR 600
The Compcut PCR 600 offers a ‘hybrid’ machining solution combining both routing and CNC milling, capable of cutting high precision ‘dog bone’ and ‘open hole’ compression test samples from an increasingly diverse range of composite materials.
The PCR 600 Router is available as a ‘complete solution package’ with a comprehensive range of cutting tools plus a suite of machining programmes, making it quick and easy to operate.
This intuitive cutting system has been specifically designed to produce highly accurate specimens and production components with an unrivalled surface finish, plus excellent parallelism and perpendicularity.
600 x 600 MM
Cleared Panel Size
5,000 to 50,000 RPM
Max Spindle Speed
3KW S1 5KW max
Spindle Power
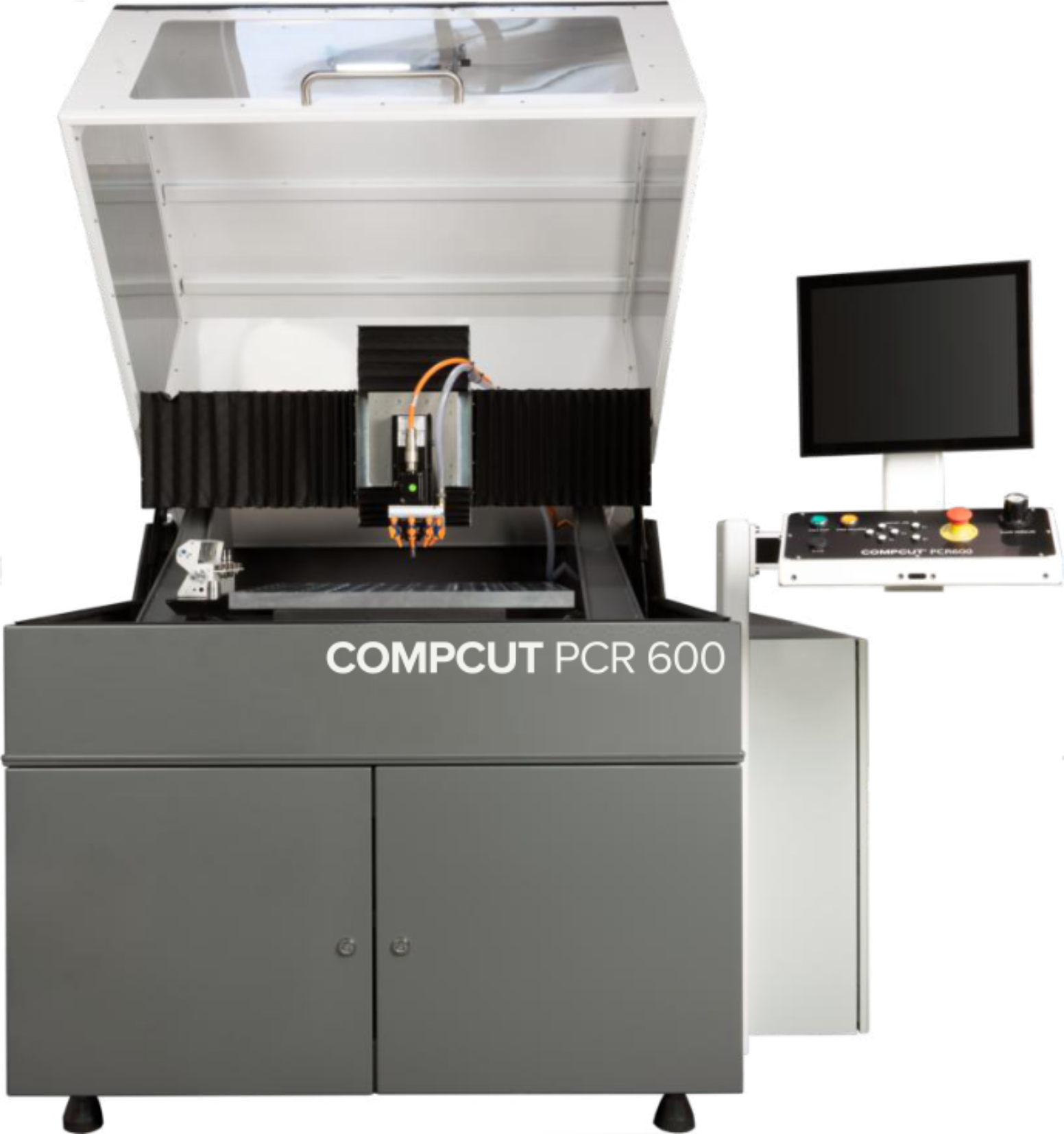
FAST & PRECISE
- Zero backlash ballscrews with precision guides on each axis.
- Rapid speeds up to 3000mm/m*
ACCURATE & REPEATABLE
- Test your specimens straight from the machine with unrivalled surface finish.
SAFE & SIMPLE
- Your engineers can cut with confidence; Our fully enclosed work area protects from dust and spray
TOOLS & MATERIALS
Compcut have developed a comprehensive range of cutting tools and processes to support machining across a wide variety of composite materials.
- Carbon Fibre Reinforced Polymer (CFRP)
- Ceramic matrix composites (CMC)
- Aluminum matrix composites
- Thermoplastic Composites TPRC
- GRP
- Plastics
- Aramid Fibre composites
- (See brochure for more info on tools)
-
PROGRAMMING
Pre-programmed with part-programs for supplied fixtures, or to customers’ specific requirements.
- G Code programming
- CAD – CAM workflows for various CAM packages
- Drag and Drop Specimen layout creation – Coming soon.
JIGGING, WORK HOLDING FIXTURES
The PCR allows for a full range of solutions, from a fully wet or dry vacbed, to custom made fixtures and tooling.
Common parts include:-
- CAI’s
- Tensile Dog Bones
- V-Notches
- Bearing Response
- Specimens
- Open Hole Specimens
SPECIFICATIONS
Material Capacity | |
---|---|
CLEARED PANEL SIZE | 600X600MM |
MATERIAL THICKNESS/CUT DEPTH* |
TBA MM – SUBJECT TO TOOL |
AXIS TRAVEL X, Y, Z |
620, 620, 130 MM |
BRIDGE / TABLE CLEARANCE |
130 MM |
COOLANT CAPABILITY |
FLOOD COOLANT WITH BAG FILTER |
Enclosure | |
ENCLOSURE |
FULLY ENCLOSED – EXTRACTABLE |
Spindle | |
SPEED | 5,000 TO 50,000 RPM |
SPINDLE POWER | 3KW S1 5KW max |
TOOLHOLDER COLLET |
HSK-E25 ER16 |
AUTOTOOL CHANGER | 5 STATION |
TOOL SHANK | 1 – 10 MM |
CONCENTRICITY / RUNOUT |
<1uM |
Speeds | |
RAPID SPEEDS X,Y,Z | 300MM/S |
CUTTING SPEEDS | 0.1 – 100MM/S |
Accuracy, Perpendicularity, Parallelism | |
TYPICAL SPECIMEN PERPENDICULARITY | TBA |
TYPICAL SPECIMEN PARALLELISM / 100MM* | TBA |
TYPICAL SPECIMEN PARALLELISM / 300MM* | TBA |
TYPICAL SPECIMEN PARALLELISM / PANEL | TBA |
TYPICAL SPECIMEN DIMENSIONAL ACCURACY |
TBA |
TYPICAL SPECIMEN PARALLELISM Z PLANE |
TBA |
External Dimensions: (W)x(D)x(H) | |
WIDTH* | 1830 MM |
DEPTH* | 1900 MM |
HEIGHT* | 1770 MM |
Required Services | |
POWER | 415V 3PH 32A |
AIR – DRIED & FILTERED | 70- 100 PSI |
EXTRACTION | APPLICATION SPECIFIC |
COMPOSITE TEST & EVALUATION
A YEAR ON: COMPCUT PCR300 PUT THROUGH ITS PACES
Composite Test & Evaluation (CTE) based in Honiton is a leading test centre for composites and other non-metallic materials. The company has over 10 years experience in the aerospace & related sectors and from its specialist, highly equipped facilities offers a reliable, technically accurate & cost effective materials qualification service.
We asked Paul Yeo the CEO at CTE the following questions, to understand his thoughts about the Compcut PCR router (following a year of operation at their Honiton test centre).
What made you choose the PCR 300?
We wanted to be able to expand our cutting capability from the typical rectangular specimens cut on the plate saw, to be able to do V-Notch specimens to ASTM D5379/D7078, and also to the machining of dogbone shapes, which we had to outsource until we received the router.
What tasks does the machine undertake on a routine basis?
Machining of V-Notch specimens to ASTM D5379/D7078, Machining of Dogbone specimens to ISO 527-2 and ASTM D638. We also use it for hole drilling of open hole ASTM D5766 and ASTM D6484 specimens and bearing specimens to ASTM D5961.
How has it performed over the last 12 months?
Very well; it has reduced our turn around times for the standard tests as we no longer need to outsource this work.
How easy was it to learn and use (was all the required tooling and programming in place – so you could use it as soon as it arrived)?
The router was supplied with all the tooling and programs we needed for our initial standard tests. We requested this capability when we purchased the router. The only slight negative was that the user interface could have been better to use, hence we are looking forward to seeing the updated version of this interface, as it’s currently in development and expected soon.
What was the service and support like?
Excellent as always and very helpful in modifying methods when necessary, and supporting us during the use of the router.
Has it met your expectations?
It has met our expectations. Moving forward we are looking forward to adding a vac-bed capability on this machine, which will help us to improve our knowledge of the software, and in- turn be able to machine more bespoke specimens as and when the needs arise from our customers.
In what ways has it benefited operations? What’s been the main impact of this machine in your organisation?
It has allowed us to significantly reduce our turnaround times, as we are now able to machine specimens within hours rather than having to wait days for them to be outsourced for machining.
What are your thoughts after a year of use?
We are very happy with the machine, as it has allowed us to reduce our outsourced specimen machining to almost zero, and we look forward to expanding its use over the next twelve months.