The Material Challenge
Previously, our team at Sharp & Tappin worked closely with the Materials Testing Team at the National Composites Centre (NCC) in Bristol, in preparation to unveil a series of planned cutting trials utilising samples of Ceramic Matrix Composite (CMC) materials.
The challenge consisted of a series of cutting tests for Sharp & Tappin’s new Compcut materials cutter. Aiming for the most efficient and exquisite finishes to practical and exploratory shapes, while testing the machines’ versatility and adaptability in cut quality. From recent trials, Compcut routers and saws had delivered a fast performance. The large format Compcut 1000 saw cutting at speeds of 125mm/s—a figure that would be used to judge how comparable CMC materials were cut effectively.
The Tested Material
Ceramic Matrix Composites are a sub-group of composite materials as well as ceramics, made from embedded ceramic fibres within a ceramic matrix. Reinforcing fibres can be added to improve CMC properties including Carbon and Silicon Carbide. As well as providing extreme heat resistance to other composite alternatives—remaining stable at temperatures above 1,800oF—CMC is lightweight and incredibly stable. Although its compressive strength is less than traditional ceramics, and delamination is prone to occur, CMC materials are nonetheless applied in a wide range of industrial uses. Such as brake systems and heating elements that must withstand high temperatures, and combustion engines like turbines and rocket propulsion components. The skill of being able to finely cut these materials opens the door for application in a plethora of energy and power spaces within the aerospace and electronics industries.
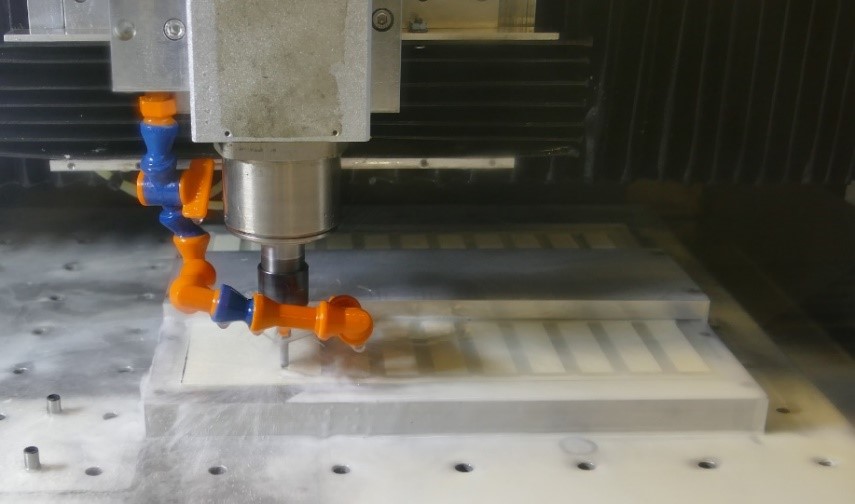
NCC had undertaken cutting of its composite materials with Sharp & Tappin’s Compcut 200 saw; meeting specific requirements of its many clients, while highlighting the capability of Compcut’s range to produce easy and efficient CMC cut products. The latest challenge was met when NCC had a requirement to cut complex shapes far from the ease of perpendicular, rectangular parts. The task was up to the latest pre-production machine in the Compcut line: Sharp & Tappin’s Precision Composite Router 500 (PCR), to cut dog-bone shaped specimens from CMC.
The Compcut Achievement
The results showed similar levels of clean finishes as from the Compcut saws, and now Sharp & Tappin is ready to expand the challenge onto further materials to fully test the durability and effectiveness in precision cutting of advanced composites.
The Compcut PCR 500 is a safe and compact machine, delivering fast, high power cutting at 100 mm/s from within an enclosed and extractable casing. Out-performing Compcut saws that only achieve cutting speeds of 40 mm/s, the Compcut PCR 500 offers further benefits with accurate 3-axis capability, allowing for more detailed and complex designs to be viable from a wide range of advanced materials.
Other benefits extend to the cost-effective manufacture of the router. Performing with advanced CNC capabilities, the Compcut PCR 500 presents an improved cutting suite in the structure of a vertical machining centre, reducing its size that some on-market CNC cutters cannot achieve, often taking up large floor spaces. Although compact, the machine continues to perform at rapid speeds of 300 mm/s, with a high-speed spindle, large work bed, and flood coolant capability with a bag filter.
Our Latest Challenge
Previously showcased at the Advanced Engineering Show, the Compcut PCR 500 has elevated the number of possibilities for Sharp & Tappin and NCC with its Ceramic Matrix Composite challenge, evoking the innovative creativity that advanced composites bring to the ever-changing landscape of today’s construction, aerospace, transport, and other relevant industries. Sharp & Tappin’s latest line-up of PCR cutters includes the ‘entry-level’ PCR 300, PCR 600, and the large format PCR 1200.
Compcut machines produce consistent, highly accurate test samples that are a critical part of the production process with composites—a task that is usually inconvenient, slow, dirty, and with a high-risk factor. Many top engineering businesses and academic institutions have already adopted the Compcut line for a more efficient composite cutting solution for essential test samples.
Now, Sharp & Tappin is looking for its next challenge.
We are encouraging material designers to question their traditional approach to cutting by submitting their composite material to Sharp & Tappin for a fair assessment of test sample quality and experience. A demonstration will take place at your desired location—the options being displayed on our website—after which a free set of samples will be provided at the end for personal sample testing. Designers can then compare the Compcut process with their current approach.
Direct benefits will be evident after the first tests, including:
- Safety of apparatus
- Clean-up after cutting
- Cutting speed
- Ease of use
- Cost-effectiveness
- Consistent accuracy
- Reduced waste and debris
Sharp & Tappin are confident of applicant satisfaction after initial demonstration. So much so that if businesses are pleased with the results, a member of the Compcut team will be in touch to take additional information and present a comprehensive business case to justify the necessary capital expenditure.
Take on the Compcut Challenge
Join us at JEC World, Paris from 3rd to 5th May in Hall 6, Stand S60, and follow us on LinkedIn, Facebook, Twitter, Instagram, and YouTube for the latest Compcut Challenge news.
To take part in the Compcut Challenge, register here: www.compcutacm.com/compcut-challenge.